«ПРОТОН-ПМ» и ПНИПУ повысили прочность сплава для ракетных двигателей
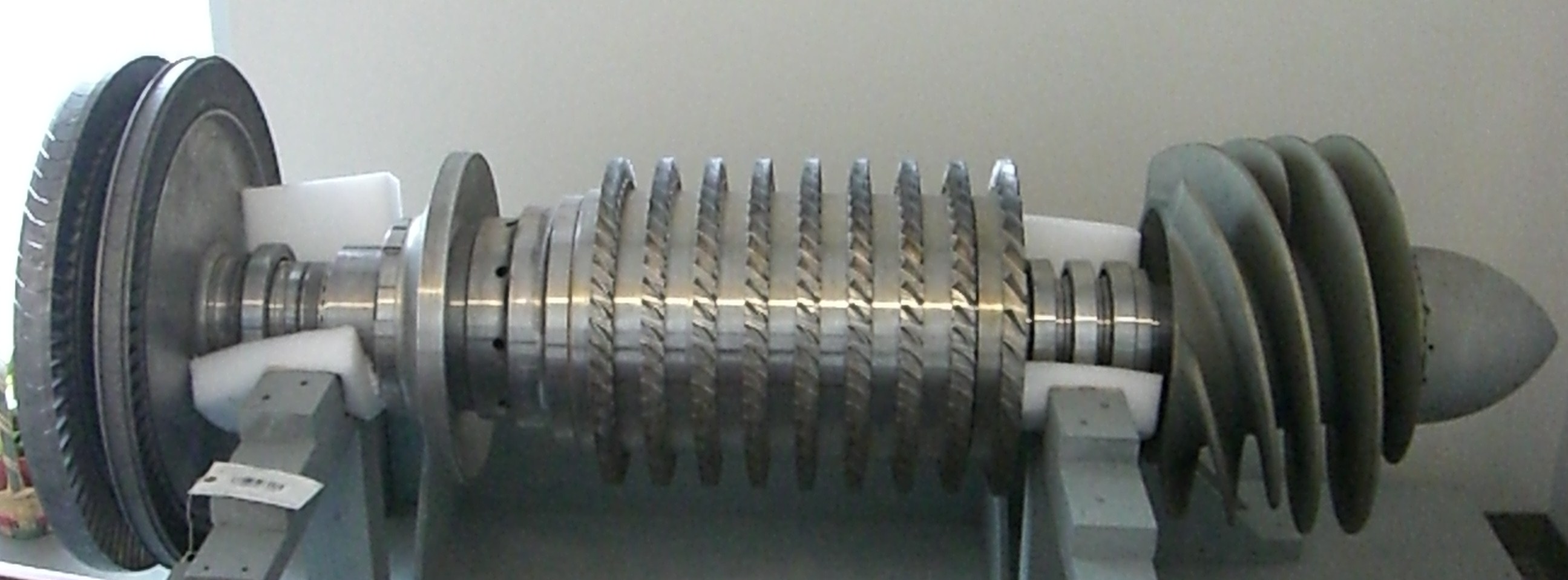
Технологию, позволяющую улучшать свойства отливок деталей турбин и повышать их прочность на 10%, разработали специалисты АО «Протон-ПМ» совместно с учеными Пермского национального исследовательского политехнического университета (ПНИПУ), 7 мая сообщает пресс-служба вуза.
Турбонасосный агрегат является «сердцем» ракетных и авиационных двигателей. Он работает при высоких оборотах, давлениях и температурах, что обуславливает повышенные требования, предъявляемые к используемым при его изготовлении материалам.
Важнейшие детали турбонасосного агрегата льют из жаропрочных никелевых сплавов, в структуре которых присутствуют карбиды (соединения металлов с углеродом), которые обеспечивают прочность деталей при высоких температурах. К их числу относится присутствующий в отливке карбид титана.
Материаловеды знают, что механические свойства сплава могут снижаться из-за несовершенства его кристаллического строения. При затвердевании расплава в его микроструктуре образуются кристаллы разного вида — округлые, называемые зернами, и ветвистые — дендриты.
Слабые места сплава обычно располагаются между осями дендритов и по границам зерен, там, где в процессе охлаждения жаропрочного никелевого сплава углерод связывается с титаном и образует карбиды.
Специалисты АО «Протон-ПМ» (входит в интегрированную структуру ракетного двигателестроения АО «НПО Энергомаш» Госкорпорации «Роскосмос») совместно с учеными ПНИПУ предложили для повышения прочности деталей из жаропрочных никелевых сплавов, улучшения их качества и «выносливости» вводить в них модификатор на основе карбонитридов с сохранением химического состава сплава.
Заместитель главного металлурга АО «Протон-ПМ», магистр ПНИПУ Максим Рожков пояснил суть разработки:
«Существующие варианты позволяют сделать деталь прочнее либо с помощью технологических приемов, либо изменяя химическую формулу, что влияет на их характеристики. Наше решение помогло стабилизировать механические свойства жаропрочного никелевого сплава за счет ввода модифицирующего состава. Он повышает показатели прочности на 10–20% по сравнению с уровнем, заявленным конструкторами. Вместе с тем химическая формула сплава остается неизменной».
Этот модифицированный состав состоит в отношении к массе шихты из 0,25% алюминиевой стружки, 0,25% титановой губки и 0,5% мелкодисперсного порошка карбонитрида титана.
Компоненты этого состава перемешиваются, спрессовываются в таблетку, которую затем вводят в расплав при температуре 1520 °C. Далее нагревают его до 1650 °C и выдерживают 2 минуты. Затем температуру расплава снижают до первоначальных 1520 °C и заливают в керамическую форму.
Модифицированный таким образом сплав был испытан на растяжение при разных температурах, исследована его ударная вязкость (способность поглощать механическую энергию в процессе деформации) и проведен ряд других исследований.
«Мы установили, что комплексное модифицирование сплава повысило предел прочности на 10% и ударную вязкость на 30% по сравнению с серийным сплавом. Свойства улучшились за счет равномерного распределения карбидных фаз по всему объему сплава. Такое упрочнение приводит к измельчению кристаллической структуры металла и снижению микропористости, что положительно сказывается на эксплуатационных характеристиках деталей и готовых изделий», — рассказал главный металлург АО «Протон-ПМ» Алексей Шумков.
Результаты исследования новой технологии авторы представили в статье «Модифицирование жаропрочных никелевых сплавов типа ЖС мелкодисперсными порошками», опубликованной в журнале «Литейное производство» № 2 за 2024 год.
Применение предложенной технологии при производстве деталей ракетных и авиационных двигателей повысит их прочностные характеристики, что доказала ее проверка в заводских условиях в АО «Протон-ПМ».