Ученые ЮУрГУ создают цифровые двойники остаточного ресурса оборудования
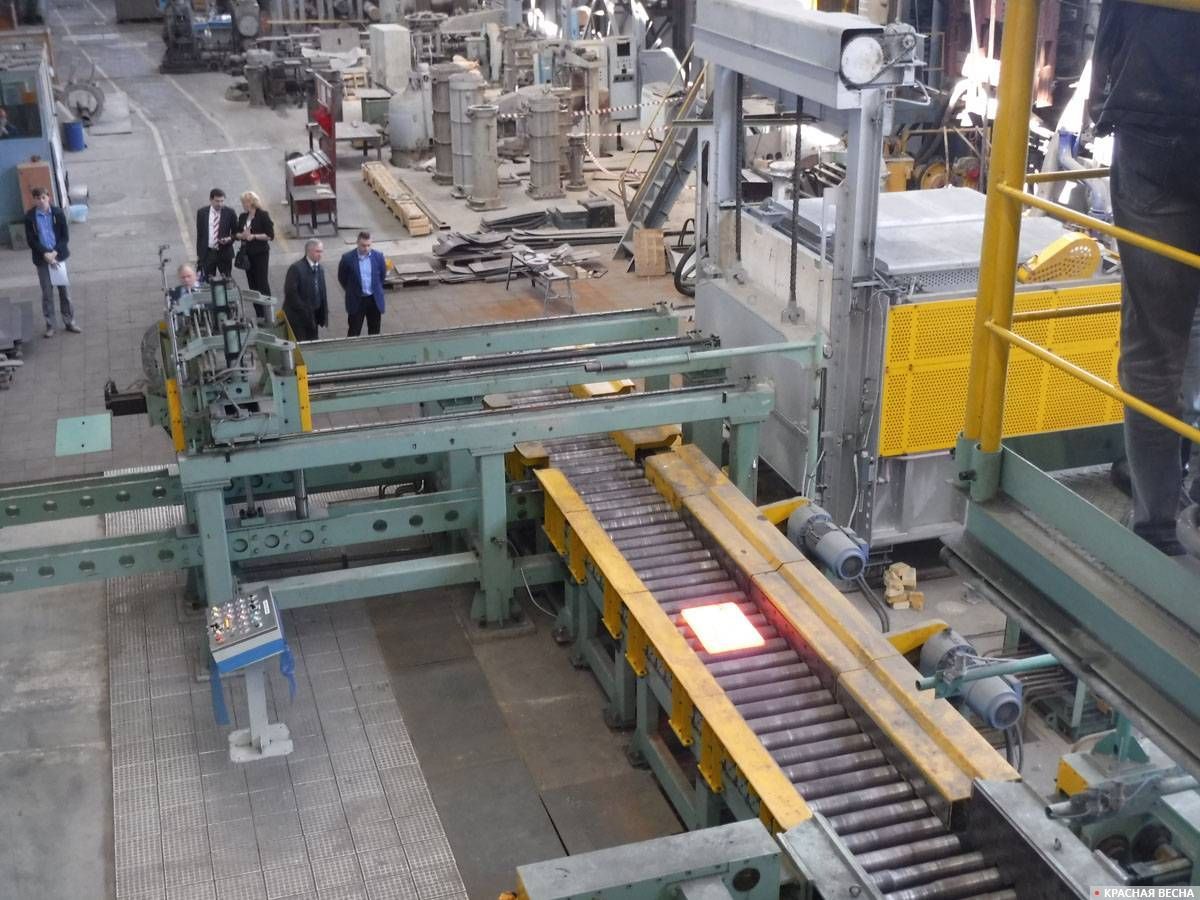
Новую методику предсказания образования трещин на элементах производственного оборудования разработал научный коллектив НИИ опытного машиностроения Южно-Уральского государственного университета (ЮУрГУ), 25 апреля сообщает пресс-служба университета.
Прогноз образования трещин в металлургическом или машиностроительном оборудовании по этой методике выполняется с помощью создания цифровых двойников остаточного ресурса этого оборудования. Разработка и исследование новой методики велось в рамках стратегического проекта «Интеллектуальное производство».
Длительное воздействие вибраций различной степени интенсивности при эксплуатации оборудования на производстве приводит к образованию микроповреждений конструкций. Накапливаясь, они образуют трещины, которые могут привести к разрушению оборудования и вызвать аварийную ситуацию.
Оснащение важного оборудования на производстве различного рода современными датчиками позволяет осуществлять прогнозную диагностику и оценивать техническое состояние такого оборудования с помощью специализированных алгоритмов и цифровых моделей.
Новая методика ученых ЮУрГУ, которая предсказывает образование трещин элементов оборудования, повышает точность прогноза их долговечности за счет непрерывного мониторинга, осуществляя прогнозирование остаточного ресурса конструкций в режиме реального времени.
Их методика оценки долговечности использует реальные данные датчиков без обычной в таких случаях предобработки — традиционного разделения на кусочно-стационарные и переходные участки.
Учет методикой нестационарности случайных процессов нагружения конструкций позволяет вести мониторинг и прогнозирование остаточного ресурса с повышенной точностью оценок остаточного ресурса — более чем на 20% по сравнению с традиционными методами оценки.
Руководитель исследования, старший научный сотрудник Центра виброиспытаний и мониторинга состояния конструкций, кандидат технических наук Алексей Ерпалов пояснил суть нового решения:
«Реальные показания датчиков — это нестационарный сигнал, то есть со случайно изменяющимися во времени характеристиками, наличием всевозможных трендов, ударных импульсов и др. Нам удалось применить современные методы анализа нестационарных процессов к физическим моделями долговечности».
Исследование нового метода велось на современном оборудовании Центра виброиспытаний и мониторинга состояния конструкций, в том числе с использованием электродинамических вибростендов LDS, разнообразных датчиков (тензорезисторы, акселерометры, датчики виброперемещений), лазерного виброметра Polytec и др.
«Наше исследование междисциплинарно. Мы используем современные методы эмпирической декомпозиции и обработки сигналов, адаптируем их к современным методам оценки долговечности. В процессе такого „симбиоза“ и рождаются новые идеи и принципиально новые подходы», — рассказал Алексей Ерпалов.
Разработчики подчеркивают, что внедрение цифровых двойников остаточного ресурса оборудования станет для прокатных цехов металлургических компаний возможностью предупредить аварийные остановки оборудования за счет проведения своевременных ремонтно-восстановительных работ.
Кроме того, у технологов появится возможность заранее определить, как изменится ресурс оборудования при изменении технологического процесса производства, с помощью проведения виртуальных испытаний, имитируя показания датчиков, установленных на оборудовании.