Ученые ПНИПУ помогут производителям избежать брака деталей из композитов
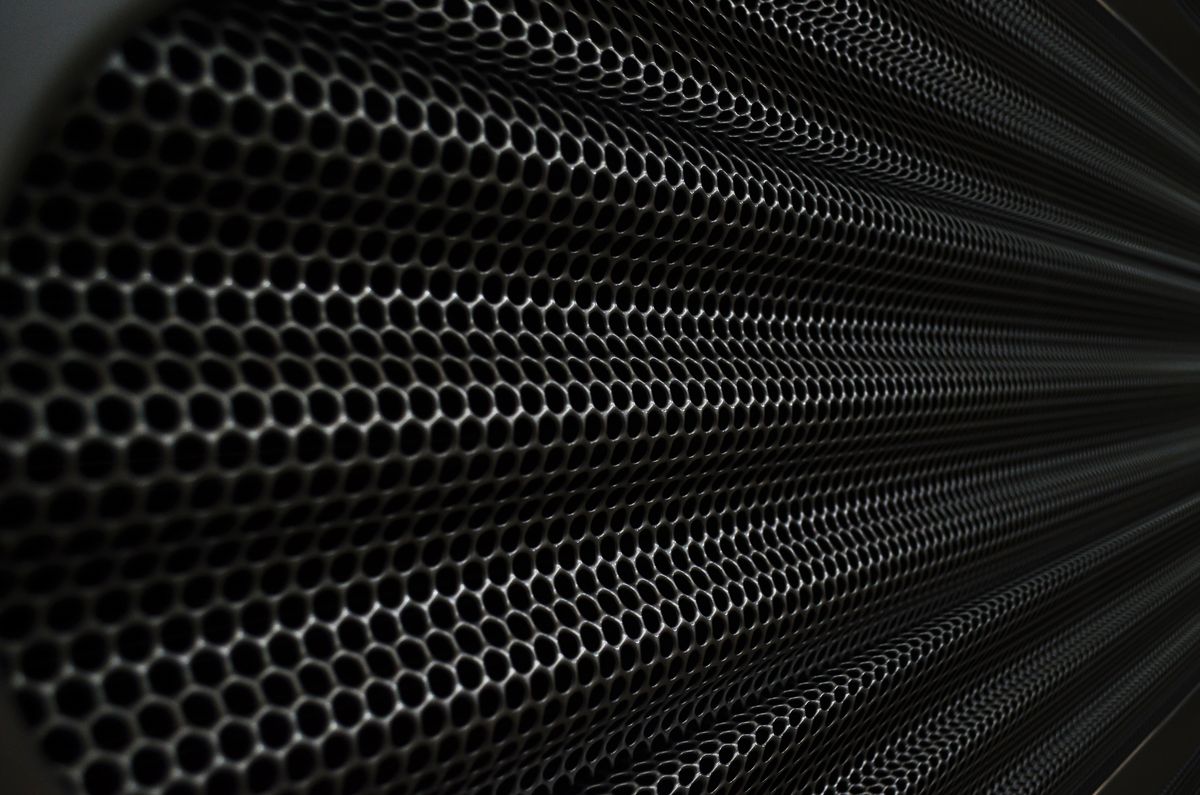
Оптимальные режимы предварительного формования заготовки, обеспечивающие лучшее качество толстостенным изделиям из композитных материалов, определили в ходе исследования ученые Пермского национального исследовательского политехнического университета (ПНИПУ), 19 марта сообщает пресс-служба вуза.
В последние годы промышленность стала активно использовать для толстостенных конструкций композитные материалы на основе полимера и непрерывных угле- или стекловолокон. Популярность такому материалу обеспечивает его легкость и прочность, которая позволяет использовать его для изготовления работающих в условиях высоких нагрузок деталей, таких как элементы самолетов, ракет и подводных лодок, лопасти ветрогенераторов, газовые баллоны и др.
Конструкции из композитных материалов с волокнами углепластика создаются в автоклаве. В эту печь устанавливается специальная форма, повторяющая контуры будущей детали, в которую предварительно выкладывают слои материала из волокон и смолы — препреги. Затем под воздействием высоких температуры и давления смола затвердевает, а слои плотно соединяются друг с другом, образуя готовое изделие.
Однако такая технология в случаях, когда толщина стенок изделия велика, не может обеспечить равномерное уплотнение материала, что приводит к возникновению различных дефектов — пористости и волнистости слоев. Чтобы исключить их появление, ученые Пермского Политеха предложили проводить подформовку при определенном режиме.
На этапе подформовки после выкладки слоев в форму перед окончательным отверждением препрег немного прогревают и уплотняют, чтобы смола лучше распределилась по заготовке. Эта операция улучшает качество и характеристики изделий, но для получения наилучшего качества нужно знать, сколько раз ее нужно повторять и какие температура, давление и длительность при этом нужны.
Оптимальные режимы процесса подформовки слоистых пластин углепластика ученые Пермского Политеха установили экспериментально. Они нагревали образцы, выдерживая их при определенной температуре в течение 10 минут, и затем охлаждали до 30 градусов. После чего определяли уплотнение материала по толщине пластин и проводили испытания образцов на прочность.
Ведущий инженер Научно-образовательного центра авиационных композитных технологий, аспирант кафедры механики композиционных материалов и конструкций ПНИПУ Артем Сыстеров рассказал о полученных результатах:
«Мы установили, что материал максимально уплотняется (на 0,75 мм) при температуре 80 градусов. Это происходит из-за снижения вязкости смолы в составе препрега, что способствует ее выходу из объема заготовки и исключает появление воздушных прослоек между слоями. Близкие значения уплотнения (0,66 мм) достигнуты при температуре в 70 градусов. При работе автоклава под давлением в 5 атм средняя продолжительность составила 1 час 43 минуты».
То есть для толстостенных заготовок оптимальный режим подформовки — это предварительный прогрев в автоклаве при 70–80 градусах и давлении 5 атм, что обеспечивает более плотное прилегание слоев, предотвращая образование дефектов, пористости и неравномерности структуры материала.
Кроме того, исследователи установили, что проведение дополнительной подформовки при высокой температуре увеличивает плотность слоев материала до значения, близкого к толщине монослоя сформованного углепластика. Проведение от 2 до 5 таких операций позволяет заготовке сохранять прочность при высоких нагрузках (78–80 МПа) в процессе эксплуатации.
Однако если подформовка выполняется после 14 дней хранения подготовленного препрега, а потом проводится 5 раз и больше, его прочность окажется ниже, что говорит о «старении» материала, который потерял свои свойства.
Таким образом, проведенное учеными ПНИПУ исследование позволило установить оптимальные режимы формования заготовок, которые повысят скорость и качество изготовления промышленных толстостенных конструкций из композитных материалов.
Полученные результаты исследователи представили в статье «Влияние температурных режимов подформовки на свойства толстостенного углепластика», опубликованной в журнале «Вестник ПНИПУ. Машиностроение, материаловедение», 2024 год.